Home builder software news headlines include four factors to consider when selecting a house wrap product.
While house wrap continues to be one of the best investments a builder can make for themselves and their home buyers, not all house wraps are created equal. This article will cover four factors builders should consider when choosing a house wrap for their next project.
With the continued rise of green and sustainable construction, builders across the country are addressing moisture and air management through careful product specification and smart building processes—even down to the selection of house wrap. A high-performing house wrap with optimal breathability can help improve a home’s durability, indoor air quality and even help reduce utility costs.
Home builder software news headlines help builders choose the right house wrap.
- Ability to Serve as an Air Barrier
Did you know the average 2,500 square-foot house has more than a half mile of cracks and crevices that are open to wind and wind-driven rain? As an air barrier, house wraps reduce convective wind washing against sheathings and air infiltration into stud wall cavities. As part of an air barrier assembly, a house wrap can reduce drafts, increase comfort and reduce energy use by decreasing the amount of non-conditioned air entering and exiting conditioned wall cavities. In fact, according to the Department of Energy and ENERGY STAR®, continuous air barriers can reduce energy cost as much as 15% to 20%. - Jobsite Durability
To be effective, a house wrap must remain in place after installation. Many house wraps can be torn by heavy winds or ripped by the rigors of the job site. This requires re-installation or significant repair to ensure the best functionality of air and water holdout. This costs the builder profits and delays the project. House wraps with excellent tear resistance minimizes this problem.UV stability is also vital to the performance of a house wrap. Even limited exposure to ultraviolet rays causes some house wrap to deteriorate. Technologically savvy manufacturers have begun to place UV inhibitors in the coating and fibers of their house wrap products. While most builders cover house wrap shortly after installation, the prudent builder looks for a house wrap with at least a 6-month UV rating.
- Surfactant Resistance
Surfactants found in wood tannins, cedar oils, and turpentine within some cladding, as well as soap solutions, can reduce the surface tension of house wrap, consequently decreasing its water holdout. Therefore, builders should look for the house wrap with the highest surfactant resistance to properly protect their homes, especially when installing under vinyl and wood siding, brick, stone, and stucco. - Compatible System Option
Some manufacturers have developed a system approach, which includes compatible tapes for seaming and adhesive flashings for openings, that vastly improves the air and moisture resistance of the house wrap. One example is the TYPAR® Weather Protection System which comes with an industry-leading lifetime limited warranty that covers the cost of labor and materials, giving builders yet another level of confidence in the system.
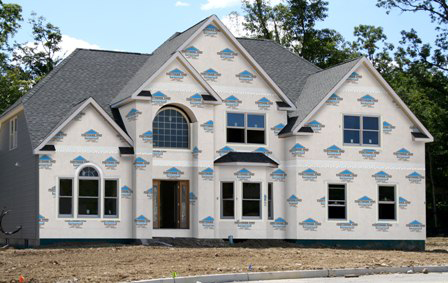
House Wrap Picture
Home builder software news headlines help homeowners, builders, engineers, contractors, and DIY enthusiasts with cost saving information for all types of building projects.
Cad Pro’s computer aided design software is an affordable and easy alternative to other more expensive CAD software programs. Cad Pro is great for creating custom home plans, building plans, office plans, construction details, and much more.
Share your designs with clients or team members using Dropbox®, Google Drive™, OneDrive®, and SharePoint®. Export files to Microsoft Word®, Excel®, and PowerPoint® with a single click.